Selection of Gear Materials:
Key Factors and Best Practices
Gears are essential components in various mechanical devices, primarily responsible for transmitting mechanical power and motion. The choice of gear materials is crucial for the performance, durability, and cost-effectiveness of the gears. The characteristics of different materials directly affect the strength, wear resistance, corrosion resistance, and machinability of gear components.
This article will explore the key factors in selecting gear materials, analyze the advantages and disadvantages of various commonly used materials, and present best practices to help engineers and designers make informed material choices during the gear design process.
Key Factors in Selecting Gear Materials
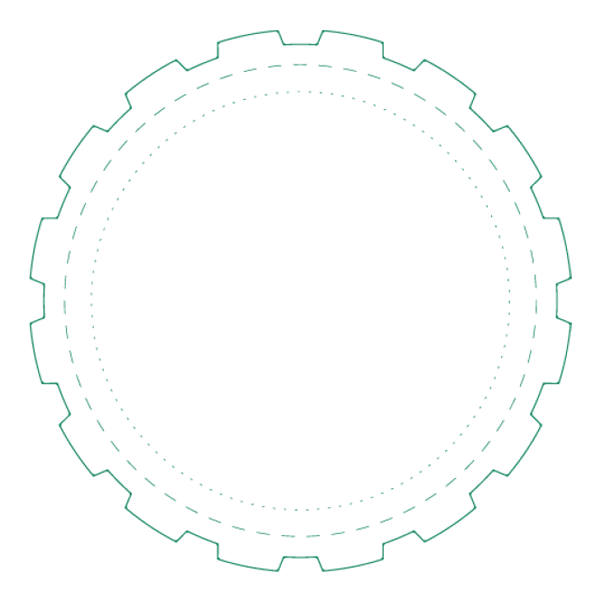
Strength and Hardness
Gears endure significant loads during power transmission, making it essential to choose materials with high strength and hardness. Insufficient strength can lead to gear deformation or breakage, while inadequate hardness may cause excessive wear. Common high-strength materials include alloy steel and carbon steel.
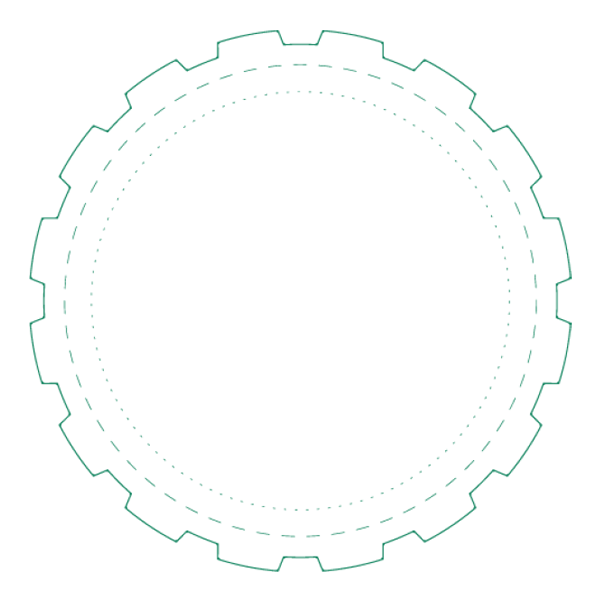
Wear Resistance
Friction occurs during the operation of gears, and the wear resistance of the material directly influences its lifespan. Wear-resistant materials can reduce wear, lower maintenance costs, and ensure the stability of equipment operation. Choosing materials with strong wear resistance, such as nickel-chromium alloy steel or high alloy steel, can significantly enhance gear durability.
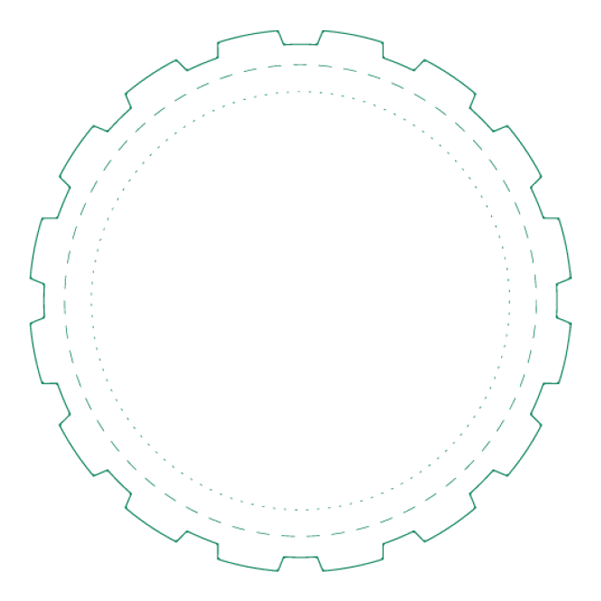
Corrosion Resistance
In certain environments, such as wet or chemically corrosive environments, gears need to have good corrosion resistance. Selecting materials such as stainless steel or plastics can effectively prevent corrosion, ensuring the long-term stable operation of gears.
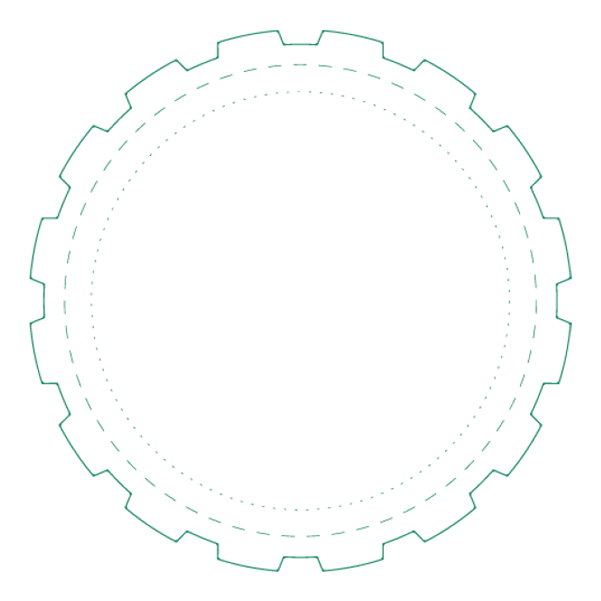
Machinability
Machinability refers to the ease with which a material can be machined during the manufacturing process. Choosing materials that are easy to machine can increase production efficiency and reduce production costs. Steel, aluminum alloys, and certain engineering plastics typically have good machinability.
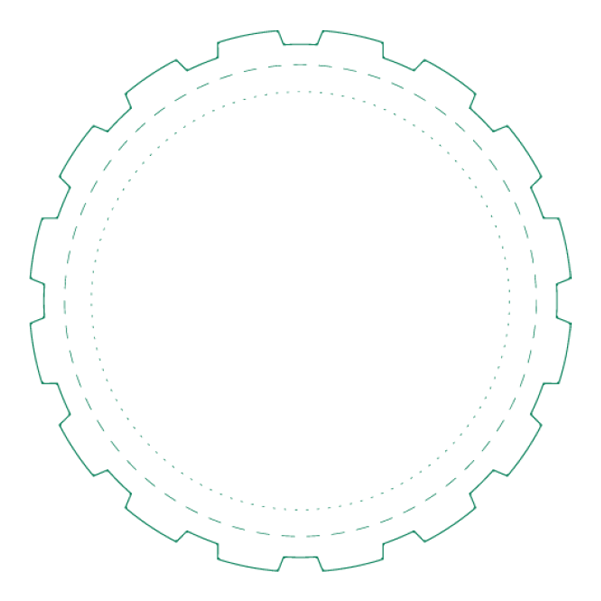
Cost Effectiveness
When selecting materials, cost must also be considered. High-performance materials may have superior properties but can come with higher costs. Engineers need to find a balance between performance requirements and budget to achieve optimal economic benefits.
Commonly Used Gear Materials
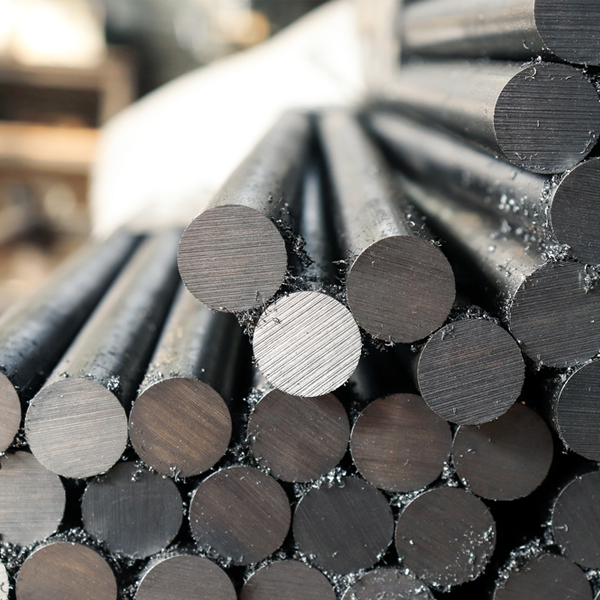
Alloy Steel
Advantages: Alloy steel offers high strength and excellent wear resistance, frequently used in gears that need to withstand high loads. Its performance can be further enhanced through heat treatment.
Disadvantages: Alloy steel tends to be more expensive and requires higher standards for the machining environment.
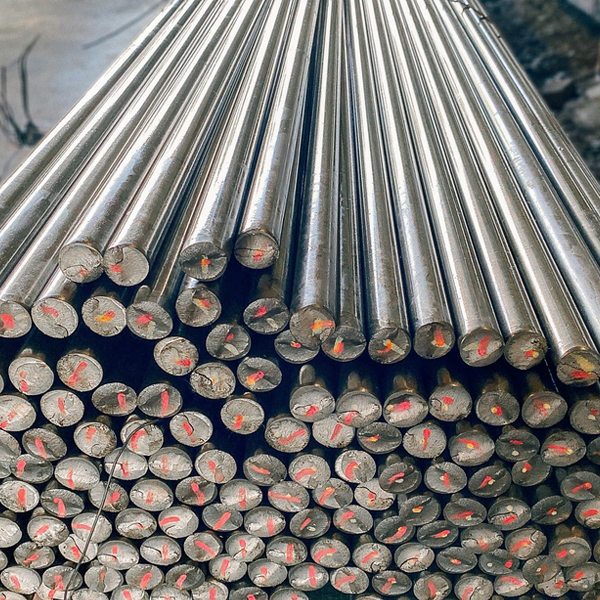
Carbon Steel
Advantages: Carbon steel is cost-effective and suitable for mass production, with good mechanical properties and ease of machining.
Disadvantages: It is comparatively inferior in wear resistance and corrosion resistance, making it suitable for lighter load applications and not ideal for corrosive environments.
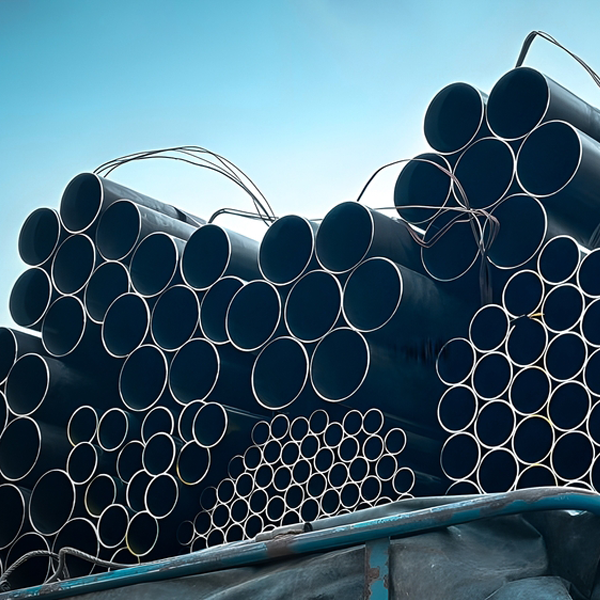
Stainless Steel
Advantages: Stainless steel features excellent corrosion resistance, making it suitable for use in wet or chemical environments, and it remains stable over long-term operation.
Disadvantages: It is generally more costly compared to carbon steel and alloy steel, with average strength and toughness.
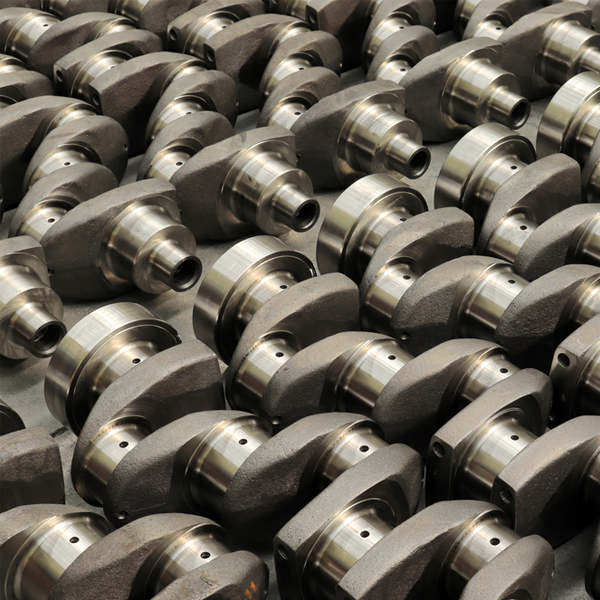
Cast Iron
Advantages: Cast iron boasts exceptional wear resistance and can handle heavy loads, while also having good machinability.
Disadvantages: It has lower toughness and poor impact resistance, making it susceptible to cracking.
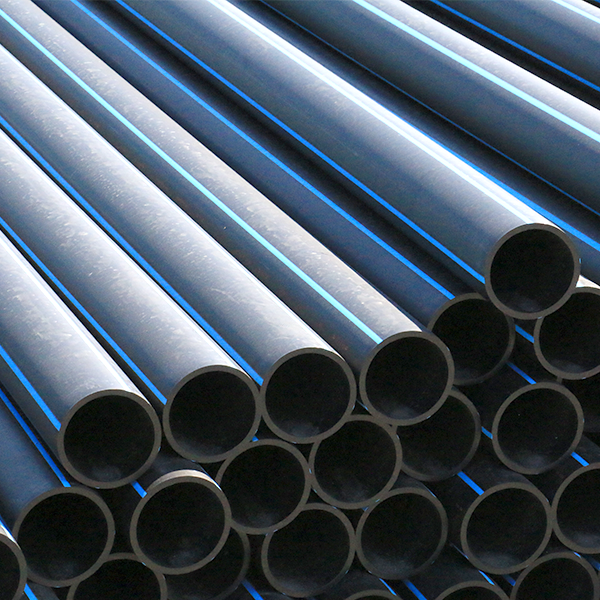
Engineering Plastics
Advantages: Engineering plastics are lightweight, resistant to corrosion, and offer good friction performance, making them suitable for low-load applications, along with good machinability.
Disadvantages: They typically have poor high-temperature performance, and their strength and rigidity are usually lower than that of metal materials.
Best Practices for Material Selection
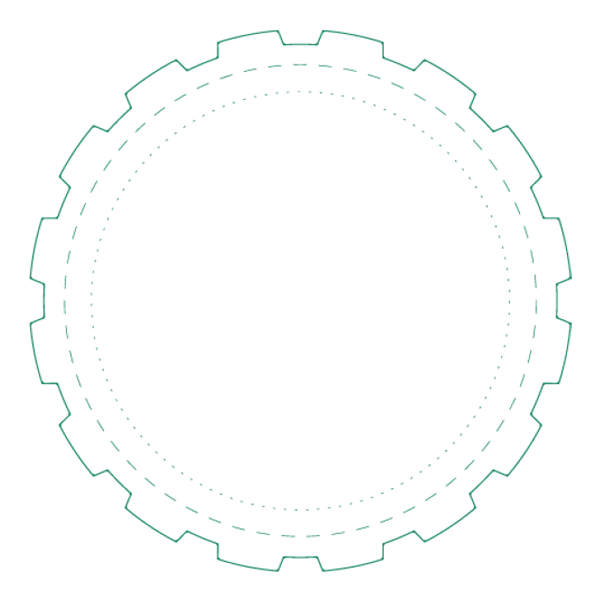
Choose Based on Application Requirements
Material selection should be based on the specific application requirements of the gears. For example, if gears will operate in a heavy-load environment, high-strength and wear-resistant alloy steel should be chosen, while gears in moist or chemically corrosive environments should utilize stainless steel or suitable engineering plastics.
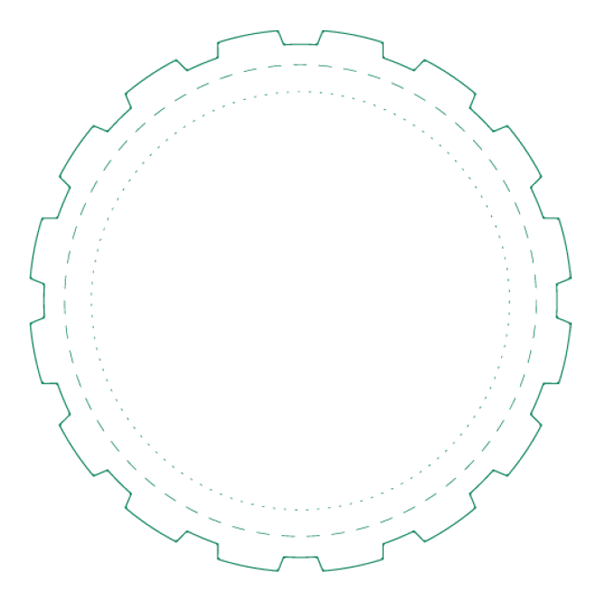
Thoroughly Consider Operating Conditions
The operating conditions of the gears are a critical basis for material selection. Environmental factors such as temperature, humidity, and chemical corrosion, as well as operating loads (static and dynamic), should be considered. This ensures that the selected material can withstand specific application conditions and maintain stability and durability.
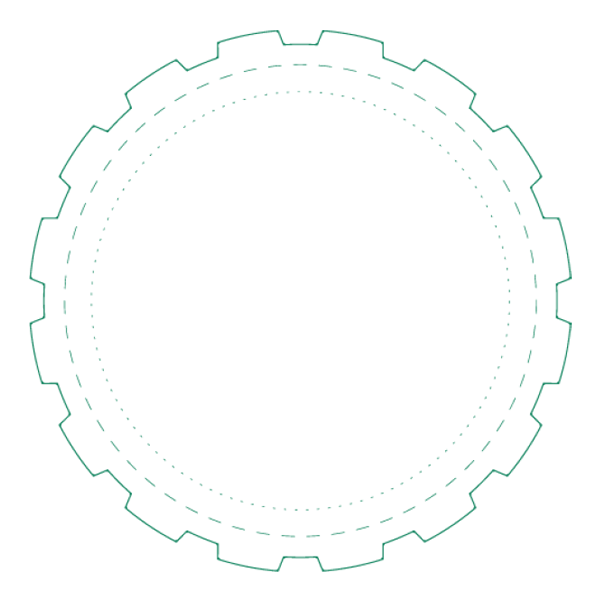
Evaluate Cost Effectiveness
When choosing materials, it is essential to further assess their overall cost-effectiveness. If the cost of high-performance materials is within budget and provides significant benefits or a longer lifespan, their selection is justified.
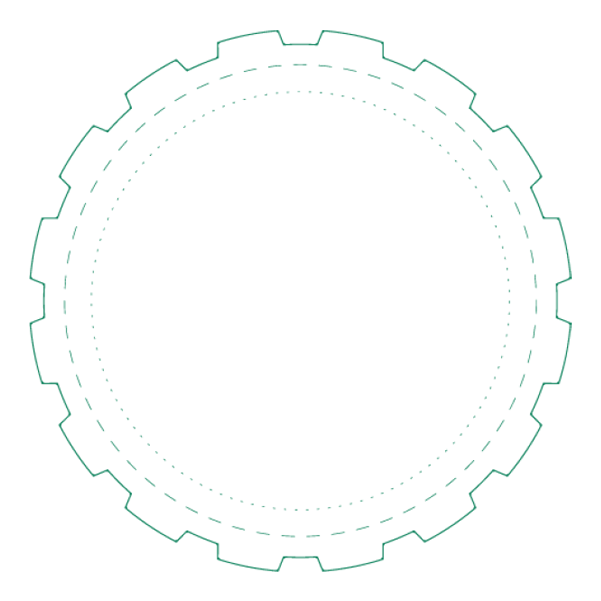
Utilize Modern Technology for Analysis
Employing digital design tools and simulation software to analyze gear performance and stress distribution can help determine the most suitable materials and design shapes. Such analysis can aid in selecting materials that perform well under specific conditions and prevent failures.
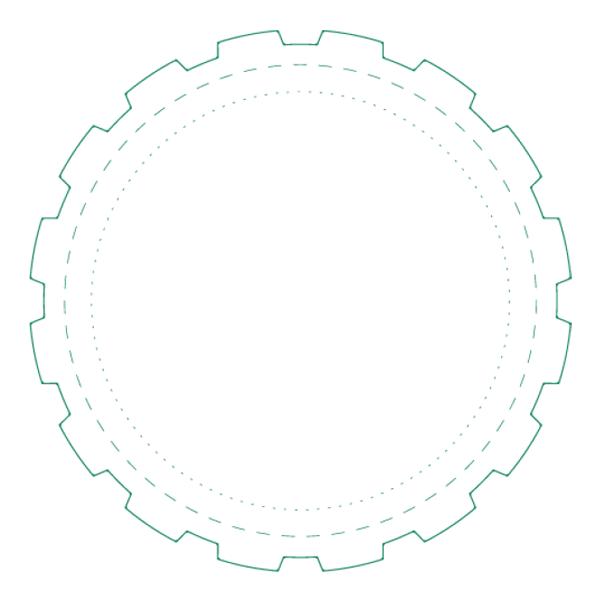
Collaborate Closely with Suppliers
Working closely with reliable material suppliers can help ensure the quality and consistency of the selected materials. The expertise and experience of suppliers can provide valuable insights and assist companies in choosing the most appropriate materials. Regular communication regarding material performance and feedback on product outcomes can further enhance the relationship and lead to improved material quality.
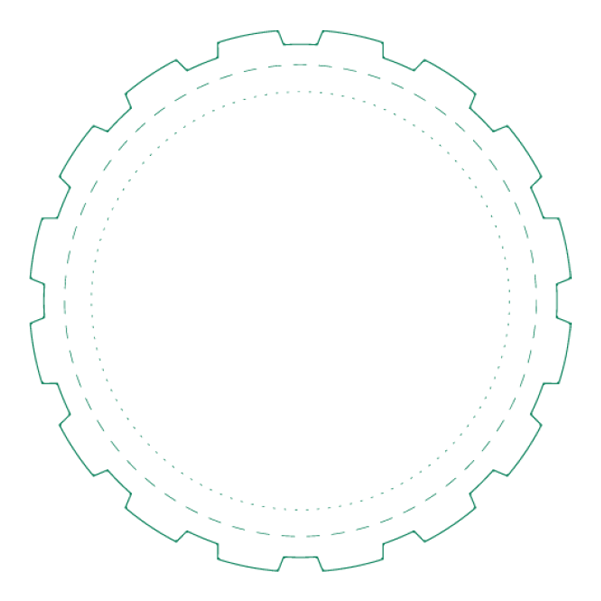
Conduct Continuous Material Testing
Ongoing material testing during the production process is crucial for ensuring gear performance. Regularly testing the mechanical properties and wear resistance of raw materials and finished gears can help verify the effectiveness of the chosen materials and make necessary adjustments. Implementing a robust testing regime will help identify potential weaknesses early in the production cycle, allowing for timely intervention and troubleshooting.
Conclusion
The selection of gear materials is fundamental to ensuring the performance and operational stability of gears. Engineers and designers must comprehensively consider various factors, including material strength, wear resistance, corrosion resistance, machinability, and cost-effectiveness. In today's rapidly evolving technological landscape, utilizing advanced design and analysis tools can significantly enhance the prediction of gear performance and lifespan.
Choosing the right materials not only improves the reliability and durability of gears but also boosts an organization's economic competitiveness in a fierce market. Through in-depth analysis and the application of best practices, gear manufacturers can adapt to market demands and drive the sustainable development of the industry. As material science continues to advance, future gears will achieve even higher performance and efficiency, presenting new innovations and opportunities for various sectors.